Why Testing Rubber Goods Is Essential to Electrical Safety
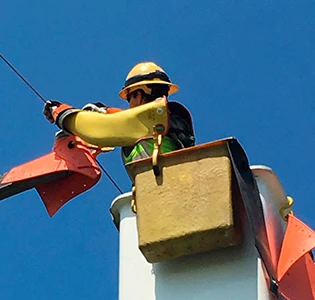
The risk of injury, and even death, from electric shock is drastically reduced by taking a few simple steps with your rubber goods. Keep up with daily inspections and cleaning, use safe storage methods, and test your equipment regularly at an experienced, accredited testing lab.
Why Rubber Goods?
Rubber goods can include gloves, sleeves, boots, blankets, line hose, and more. These are key personal protective equipment (PPE) in preventing electrical current from entering your body and causing injury or death. The Occupational Health and Safety Administration (OSHA) require rubber goods to be worn when workers are within close proximity to electrical equipment. OSHA upholds and enforces the way electrical work can be performed based on the standards issued by the ASTM F18 Committee. This committee is made up of experts in the electrical industry who set national standards and guidelines.
Getting Up to Code
Complying with ASTM standards, in addition to regular care and maintenance, reduces the risk of injury in the field. Better yet, it makes users and their companies OSHA compliant. This keeps workers safe and reduces the risk of an OSHA fine. In addition to daily inspection, proper storage, and care, rubber goods should be sent to a top-quality, North American Independent Laboratories for Protective Equipment Testing (NAIL for PET) accredited rubber testing facility. At these facilities, equipment is tested and re-certificated to stay compliant with ASTM standards (ASTM 478-09, 7.1, F479-06, 8.1.1, and F496-08, 7.1).
ASTM F496, 7.1 states that rubber gloves should be electrically tested before their first use and every six months after. Sleeves, line hose, blankets and hoods have their own specific testing cycles. Cycle dates are determined by the end user, but maximum testing intervals are mandated by ASTM. All ASTM codes are available online for review.