Vibration and Noise Control in T&D
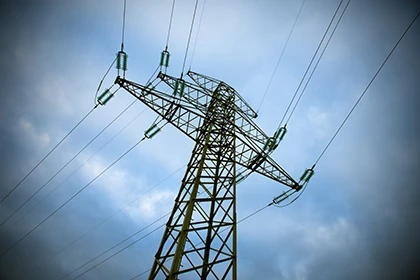
It is very often that “just putting some rubber” to isolate structures creates an inefficient or even a vibration isolation problem, without taking into account the characteristics of the whole system: such as media environment and temperature, material stiffness adjusted to the application load, surface area, material transmissibility, as well as pad design techniques, like shape factor conformity. These are fundamental to a good anti-vibration material selection and consequent noise reduction.
Through experience in T&D applications, Amorim Cork Composites has implemented a priority 4 step system approach in analysis and treatment of “noisy” equipment. Our 4 step approach focuses on the need to control vibration before it reaches the tank structure (and therefore closer to the source of vibration), impeding that structural vibrations on the tank are transformed into airborne noise through the amplitude vibration of the tank walls acting as “speakers”. Typical noise reduction gains (cumulative gains) can also be observed when designing with ACC methodology (values based on project statistics).
The Noise Conundrum
As T&D equipment become larger and more powerful, due to electrical grid complexity and natural energy sources, general tank construction relies on rigidity and stiffness to reduce the amplitude of vibrations that reach the tank wall, which are then released as airborne noise.
Whilst the increase of stiffness of the tank is achieved through the use of U-beams and profiles, this also increases the actual natural frequency (fn ) of the tank structure closing in on the gap between the disturbing frequency coming from the active part. The closeness of these two frequencies lead to an amplification in transmissibility and consequent increase in noise.
Though optimal mechanical construction is imperative for the functional characteristics of the equipment, noise level restrictions are already today part of the Utilities requirements due to end consumer demand.