Prevent Transformer Shutdown
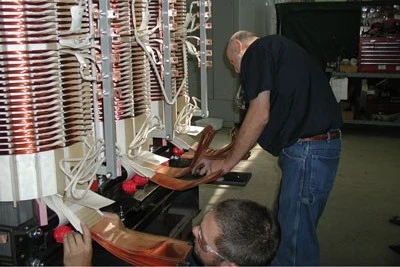
Power transformers seldom shutdown; however, if a shutdown occurs, the effects would be immediate and devastating to utility operations. According to “An Analysis of Transformer Failures” by William H. Bartley, P.E., on behalf of the Hartford Steam Boiler Inspection and Insurance Company, the average age at the time of failure ranged from only 9.4 to 14.9 years. This revelation is enough to prompt utilities to take a second look at their policies and practices when dealing with transformer failures. This article provides five suggestions that can help point utilities in the right direction.
1
USE DRY-TYPE TRANSFORMERS
Starting from the top, common types of power transformers include liquid-filled (so called because they use oil, or similar, for cooling purposes), and dry-type transformers. Given that dry-types are air-cooled, they pose less chance of leakage and fire risk.
2
EXPLORE ROUND DISC-WOUND OPTIONS
Whether wet or dry-type, the way the coils are wound around the core of the transformer greatly affects its robustness. Energy is wasted and noise is created due to increased axial forces acting at the corners of rectangular-wound transformers.
On the other hand, voltage stresses are halved between the discs of round-wound designs. Hence, round disc-wound transformers stay cooler, run quieter, present less risk of short circuit and are more energy efficient.
Beyond the improved reliability factor, the increased efficiency of the round design saves costs in real time, as the plant consumes less electricity. Some round disc-wound transformers even exceed the proposed efficiency standards for Energy Star compliance, drastically lowering utility costs for a plant.
3
CHOOSE COPPER OVER ALUMINUM
When it comes to the material used for the windings, copper is a superior conductor to aluminum because copper offers less resistance, hence less heat. Additionally, aluminum corrodes which generates heat and reduces lifespan while posing a fire hazard.
Cost is a major factor why aluminum is used as insulation in transformers. Copper currently sells for about $6,500 per ton, whereas aluminum costs around $1,700 per ton. Yet, any savings most likely evaporates under operating considerations.
Even insulation plays a major part in ensuring reliability. Temperatures can reach 200 degrees Celsius in a dry transformer on a daily basis; hence, becoming too cost-conscious on insulation can lead to disastrous consequences. Glastic fiberglass insulation or Nomex provides significantly greater protection from fires and short circuits than paper insulation. Note that Nomex is used in racing suits for Formula 1 drivers to protect them from burns.
4
REMANUFACTURED OR RECONDITIONED
Similar considerations apply when purchasing a reconditioned or a new transformer, except that the expertise of the remanufacturer plays a greater role.
At the bottom end of the remanufacturing scale are transformers that are brought in, fixed up just enough to be operational, superficially cleaned and then sent out the door. These will not hold up as well as transformers that are completely refurbished, and could leave your plant vulnerable once again.
A more completely remanufactured transformer provides far greater security against failures. There should be a complete rewinding of the primary and secondary coils along with brand new high and low voltage bus bars. While the original core can be kept 90% of the time, even it must be replaced occasionally as older steel is less energy efficient than modern core materials.
Attention to detail pays dividends in the remanufacturing process. Hand wiring ensures the highest quality. Additionally, the deburring of the copper conductor helps ensure that the insulation will not be punctured and create a short circuit.
Ultimately, any remanufactured transformer must meet or exceed all NEMA, ANSI, and IEEE standards.
5
MATCHING THE OLD WITH NEW
Too often relegated to last-minute consideration is the need to ensure that any new power transformer fits into existing switchgear—carefully duplicating “form, fit and function” as much as possible.
In order to rapidly stem losses, transformer companies exist that specialize in emergency replacement. For mission critical applications, transformers can be prepped for shipping within hours. Attention to details such as duplication of the high and low voltage bus bar spells the difference between a lengthy replacement process versus a quick, cost-effective plug-and-play solution that brings the campus back online in minimal time.
Alan Ober is Vice President of Engineering and Manufacturing for Electric Service Company (ELSCO), which specializes in providing quality new, repaired and rebuilt transformers—under emergency conditions when necessary.