Transformer Oil Regeneration and Corrosive Sulfur
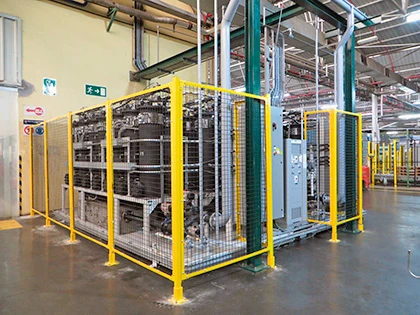
Enervac International ULC has been examining this issue for over 14 years with the help of our customers, mainly international power utilities, transformer manufacturers and transformer service companies.
TRANSFORMER OIL REGENERATION PROCESS
The principal functions of the insulating fluid are to serve as a dielectric material and an effective coolant. To perform these functions, the insulating fluid must have specific necessary qualities at the time of initial impregnation and filling at the factory, which must be maintained at the same quality level in field operation if optimum performance is to be assured.
Transformer oils deteriorate with time. High operating temperatures, the presence of oxygen and water combined with the catalytic action of the materials within the transformer, result in oxidation and cracking of the oil. The by-products of oxidation are acidic and the long-term effect of these by-products results in an exponential increase in deterioration of the transformer and its oil. The resulting sludge build- up reduces the cooling effects of the oil driving the whole decay mechanism at an increasingly accelerated rate. The acid number becomes exponential around the 0.25 mg KOH / g oil level. Preventative measures must be undertaken prior to the oil acidity level climbing to this point. Generally, the larger the transformer plate rating, the lower the acid number that triggers regeneration of the oil. Historically, Fullers Earth has been used to reduce the acid number on a one-time batch basis then disposed of. There are obvious disadvantages to this, not least the environmental impact of dumping oily waste into a landfill.
The ENERVAC E575R Transformer Oil Regeneration System provides an extremely cost-effective and environmentally acceptable method of extending transformer oil lifetime to over 50+ years!
Used oil is strained, heated and filtered prior to flowing into a bank of columns which are filled with an adsorbent media. The oil’s primary physical parameters are restored during this phase. Upon exiting the columns, the oil is passed through a degassification unit and an after-filter which restores the oil to virgin conditions. The banks of columns eventually become saturated and need to be reactivated. This reactivation is performed within the columns and does not require the adsorbent to be removed. The reactivation process typically takes 12-16 hours, during which time a second bank of columns is used to regenerate the oil. ENERVAC’s unique control system allows for 24-hour processing without having to shut the E575R down. Once reactivated the bank is again ready for processing. On average, between 300 and 500 reactivations per bank ensure that the media only needs to be changed every three to five years. Once exhausted, the media is reactivated one final time and is then discarded as a dry waste in a normal landfill - it is completely devoid of any oily waste.
The mobile ENERVAC E575R is ideally suited for processing transformers that are either energized or off-load and the skid-mounted E575R is well suited for tank farm applications.
Read full article in the SPECIAL TRANSFORMER EDITION.
Enervac INTERNATIONAL ULC advrtisement in the issue: